紙工業の価値、そして社会での評価をもっと高めたい。その願いを実現しようと、デジタル技術を積極的に取り入れる紙工会社がある。熊本県上益城郡嘉島町に本社工場を構える倉岡紙工は、紙パッケージを製造する企業だ。九州で唯一のクリーンルームを備えた紙器工場に、IoTやAI、ロボットまで導入されており、工場内で製造工程や設備を見学することもできる。時代の最先端といってもよい環境だが、倉岡紙工が実践するのは「身の丈DX」だという。それはどういうことだろうか。代表取締役社長 CEOの倉岡 和徳さんに話を聞いた。
倉岡 和徳(くらおか かずのり)さん プロフィール
1983年生まれ。熊本県熊本市出身。早稲田大学政治経済学部経済学科卒業。IBPビジネス留学 ワシントン大学コースを修了後、専門商社へ入社。香港への駐在を経験、アジア地域のサプライチェーンマネジメントをおこなう。2013年より家業である倉岡紙工を継承し、代表取締役社長 CEOを務めている(現職)。
倉岡紙工のミッションとは
倉岡紙工は1965年に創業された紙パッケージの製造企業。2013年、専門商社で働いていた倉岡 和徳さんが3代目として跡を継いだ。
「実家の倉岡紙工を継ぐ前は、日系の商社で働いていました。香港に駐在していた期間もあり、そこではアジア各国のサプライヤーさんが製造したものを集約し、全世界に向けて出荷する、サプライチェーンマネジメントが僕の仕事でした。
家業を継ごうと思ったきっかけの1つは、ハワイで同級生の結婚式に参加したときのことです。みんな口々に『熊本に帰りたいけど働ける会社がない』と話していたんです。熊本が地元で、若くて優秀な人材はたくさんいるのに、彼らの能力を活かせる職場が少ない。だったら自分でつくってやろう。そう思ったんです」
当時の工場は老朽化が進んでおり、製造環境はもとより従業員の労働環境、安全面にいたるまで、多くの問題が山積みだったという。倉岡さんが事業を継承した当時の売上は、90%が印刷会社からの下請けの仕事。さらに、紙パッケージをつくる紙工業界そのものも、ネガティブなイメージを持たれていることを知った。
「家業を継ぐとき、地元の先輩社長たちにあいさつ回りをしたんです。そこで初めて紙工業が3Kと言われていることなど、世間の人が業界に抱くネガティブなイメージを肌で感じました」
2016年に発生した熊本地震では、南高江にあった当時の本社工場が半壊。工場の中にある資材や設備も散乱し、大きな被害を受ける。地震から4年後の2020年、倉岡紙工は嘉島町に新工場を移転した。倉岡さんが確信していたのは、紙パッケージが持つ大きな可能性だ。
「出版不況のあおりを受け、印刷業は厳しい時代だといわれています。けれども、ECサイトでの需要が伸びていることなどもあり、紙パッケージの市場はむしろ好調です。
自分たちの会社を見ていても思うのが、日本のものづくりの繊細さ、真面目さは世界に誇るべき財産だということ。香港に駐在していたとき、現地の人にお土産を渡すと『この箱がすてき!ほしい!』と、パッケージを褒めてもらったこともあります。はだかのお饅頭だって、きちんと箱に収めれば立派なお土産になる。パッケージは品物に新たな価値を加える力を持っていると思うんです」
熊本で若く優秀な人たちが働く職場をつくりたい、彼らのためにも紙工業の地位を上げたい、日本人がつくるパッケージを世界に広めたい。多くのミッションを遂行するため、倉岡さんは新工場の建設に踏み切った。
倉岡紙工の工場見学を体験
倉岡紙工の工場は、製造ラインとオフィスがそれぞれ縦方向に並ぶよう配置されている。倉岡さんの案内で、工場を実際に見学させてもらった。
旧工場では3階建ての建屋に1つの工程をおこなう部屋、木型など資材を置く場所など、それぞれ動線がバラバラで大きなロスが生じていた。それらをワンフロアにまとめ、工程順に並べることで効率的な生産ラインを実現できたという。
製造ラインの異変は、廊下を隔てたオフィスが並ぶエリアから瞬時に察知することができる。どの工程で生じたトラブルかは一目瞭然のため、バックオフィスからのフォローも容易になった。
紙パッケージの製造工程は、大まかにわけると印刷、打抜、成型の3つの要素から成る。原料となる紙にパッケージのデザインを印刷し、それを専用の木型で打ち抜く。クッキー生地を型で抜くように、1枚の大きな紙から必要な部分だけを切り離す工程だ。打抜工程を経たパッケージはさらに糊や折り目がつけられ、容易に組み立てられる形に加工される。
打抜工程で出る余分な紙は回収され、リサイクル業者を経て再び原料となって工場に帰ってくる。資源を有効活用できるサステナブルなシステムだ。
パッケージの製造にはそれぞれ専用の木型が必要だ。倉岡紙工には、1枚4kg~10kgほどの重さの木型が常時3,000枚程度ある。新たな製品が生まれるたびに新たな木型がつくられるため、年々増え続ける木型の管理は大きな課題となっていた。
そこで倉岡さんは、ユニクロで在庫管理に活用されている商品タグに着目。RFID(電波を通じ非接触でIDタグと情報をやりとりする)タグを木型に付け、データベースですべての木型を管理するシステムを約1年で実現した。さらに、既存の木型を自由にシェアしてもらう木型シェアリング事業もスタート。新規顧客の獲得にもつながったという。
「以前の工場では3階に木型置き場があり、木型を取り出すだけで一苦労でした。どの場所にどの木型があるかも特定の職人さんだけが知っている状態で、まず木型を探す作業も時間的なロスになります。
RFIDタグを用いて木型をデータベースで管理するようになり、製造ラインではその工程自体がなくなりました。今ではRFIDリーダーで瞬時に木型の場所がわかりますから、誰でも素早く必要な木型を取り出し戻せる環境になっています」
新工場の一番の強みはクリーンルームを完備していること。防虫・防塵・湿度調整など徹底した衛生管理が可能となり、化粧品や医薬品など衛生面でのシビアさが要求される注文にも対応できるようになった。
出荷される商品はかなりの重量があり、以前は男性職員3人がかりでおこなうこともあったという。出荷作業の重労働を軽減しようと、新工場ではラッピングロボットを採用。現在では女性スタッフ1人でも梱包作業ができるようになった。
DX導入で「下請け企業」から脱却。企画から製造まで一元化
工場のソフトウェアの役割を果たすオフィス業務にも、積極的にデジタル技術を取り入れている。自社で企画から製造まで一貫しておこなうことで、下請け仕事が中心だった以前の経営スタイルを刷新しようという狙いだ。
2021~2022年4月にはインハウスデザイナーとして新卒者を2名採用し、社内にデザイン部門を設置した。若い世代の感性を活かして、パッケージ企画やデザインなど製品の内製化に取り組んでいる。
LED・UVインクジェットプリンターやカッティングマシンの導入により、デザイン、印刷、カットといった試作品をつくる一連の工程が企画室の中で完結。これにより、以前は2週間かかっていた試作品の製作期間を、最短1日に短縮できたという。さらに、顧客と直接やりとりすることで、紙パッケージそのものの価値も上がったと倉岡さんは話す。
「以前は印刷会社からの下請けの仕事が多く、中間業者を介して顧客が持つ『想い』や『イメージ』が薄まっていると感じていました。いまは企画から自社でおこなえるようになりましたし、生産ラインの効率化によって、小ロットでの注文にも対応できます。比較的小規模のお店だと、ロット数の多すぎる注文はコスト面での障壁が大きく、保管場所にも困る。そうしたお客さんのニーズに細やかにこたえられることが自慢のひとつです。
デジタル技術の活用で、世界に1つだけのパッケージの制作も可能になりました。オーダーメイドは付加価値が高く、単価は以前の10倍です。パッケージのクオリティを上げると、商品そのものの価値向上に貢献できる。紙パッケージが持つそうした可能性や真価を、もっと伝えていけたらと思っています」
倉岡紙工が考える「身の丈DX」とは
倉岡さんは一連の取り組みを「身の丈DX」と呼んでいると話してくれた。
「木型のIoT管理、そして木型シェアリングの事業を始める際には、熊本県の産業支援課や産業技術センターで相談に乗ってもらいました。県のIoT推進事業化補助金を受け、かかった費用約75万円のうち、自己負担は半分の約30万円で済みました。管理だけに多額の費用をかけるわけにもいきませんから、非常に助かりました。紙パッケージの製造にかかる費用のうち、木型の製作費が占める割合は約25%です。すでにある木型をシェアしてもらうことで、顧客の負担軽減にもつながっています。
DX化そのものに多額の投資が必須だとは思いません。僕らは身の丈にあったところから取り組んできただけなんです。DXの推進には、まず身近な人に相談すること、そして外部からの意見に素直に耳を傾けることが大切だと考えています。社内環境の改善、いわゆる『守りのDX』を進めるには社員の意見が不可欠です。『攻めのDX』となる新事業にはパートナーが必要です。身近な協力者をぜひ探してみてください」
1つの課題を解決すると違う景色が見えてくる、と倉岡さんは教えてくれた。
「今後は海外展開も視野に入れています。TSMCの進出で熊本は活気づいていますから、台湾で現地の紙パッケージ文化をぜひ学んでみたい。社内の業務もさらに効率化を進めたいので、営業DXにも興味を持っています」
倉岡紙工の『やりたいこと』は、こうしてひとつずつ『できる』へ近づいていく。
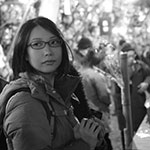
執筆
桑原 由布
1987年生まれ、熊本県出身。フリーライター、編集者。企業、観光、医療などをテーマに地元で暮らす人たちを取材している。趣味は写真撮影、生きがいは愛猫たちと過ごす時間。
※『さくマガ』に掲載の記事内容・情報は執筆時点のものです。
- SHARE